
I should have waited until then to take the photo, because it looks much sturdier that way. Note this is prior to gluing, and after adjusting for neutral, there is only 1/8" of wire protruding from the end of the CF tube. Another brass sleeve just like the one on the crank wire goes on the end of the pushrod and fits into the other end of the CF tube. I learned that the ends must be reinforced before doing anything else with it, so brass around each end to hold it together, and then rough up the interior to accept glue. While roughing up the inside I split it with ease. I cut a piece of CF tube that will fit over the above connection. Now to get to the horn with a straight angle of input. Notice the 1/2" of play it has for the side to side motion of the rod.: This is the new pushrod passing through the 3/16" brass tube that's soldered into the horn. So I cut a 5/32" long piece of the same brass that I sleeved the end of the bellcrank wire and soldered it into the top hole of the horn, giving the pushrod some side to side capability. So if I just put a z-bend and wire through the hole in the horn, it may have added some stiffness. Here's the first step:Īnother problem is that not only does the control rod move front to back, it also moves side to side because of the bellcrank motion. But the next problem is that it's still offset 1/2" to the side of the horn. The remaining length of 1.5" to the crank will be plenty stiff enough now. So I cut it off and soldered this brass tube that will fit the ID of a CF tube. Had it been straight, it would have been fine. The thing that made the link too weak was that I had to jink the wire about a half inch over to meet the horn. I'm happy with my solution and it appears to work perfectly and look pretty good too. So I toiled away for hours today figuring out my solution and implementing it. I totally underestimated how fragile the tubes are when the cut ends are not reinforced.
#Yakyak horn how to
Never worked with CF before either, and had at least one foul up that I'll know how to avoid next time. But then I would have missed yet another learning opportunity. Regarding the flexy bellcrank to flap wire, it might have worked okay, but less than perfect if I had just ignored it and kept finishing the project like I've done in the past on my little planes. That was the first thing I confirmed with a sigh of relief after I put it together.
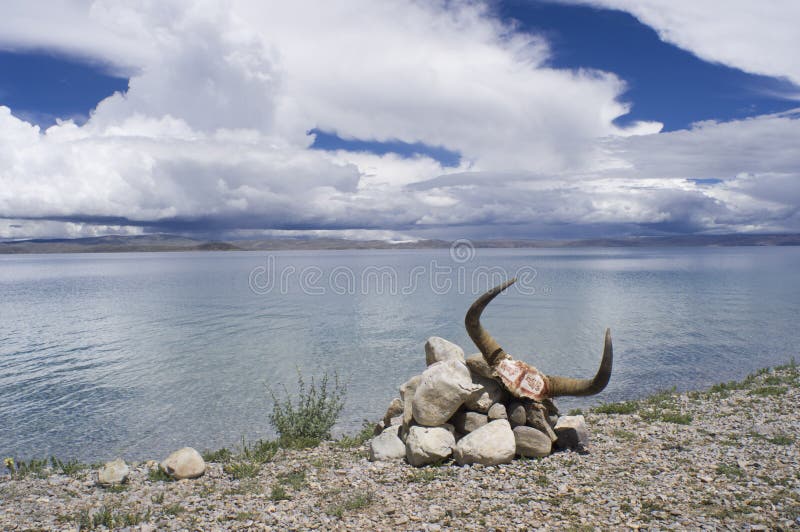
The caps on top of it as shown in the above post of the finished flap allows no vertical play. The triangular groove is allowing the hinge to have lateral "play" as it swings back and forth. I never showed a picture of the finished groove, but this is the rough-out: That's where the Lucky Box sort of grooves I cut in the flaps come in. But Sterling's mission was to make "cheap and easy" kits and this part was meant to work "well enough." A more sophisticated design would have separate control horns and rods to move each flap independently to prevent them from fighting each other for movement. With a straight TE, it's easy, plug in the coupler and everything moves freely. And yes, it won't rock up and down and stay perfectly flush, but considering the small diameter and width of the two surfaces, and the fairly short throw, there only needs to be a small amount of spare room to keep the shoulders behind each prong from binding against the TE.Īnd yes, there is no good "cheap and easy" way to connect two opposing flaps that follow such a forward swept angular hinge line. If you're talking about the slight bend between in the center of the wire between the prongs, That is so that it mates flush at the vertex of the angle of the TE. Lieven, I'm not sure exactly which part you mean, so I'll address your question two ways. I needed some nose weight so I could prop it on its nose to work on it. No, the Fox is just all oily and on an engine mount. I'll come up with a strong and not too funny looking fix.
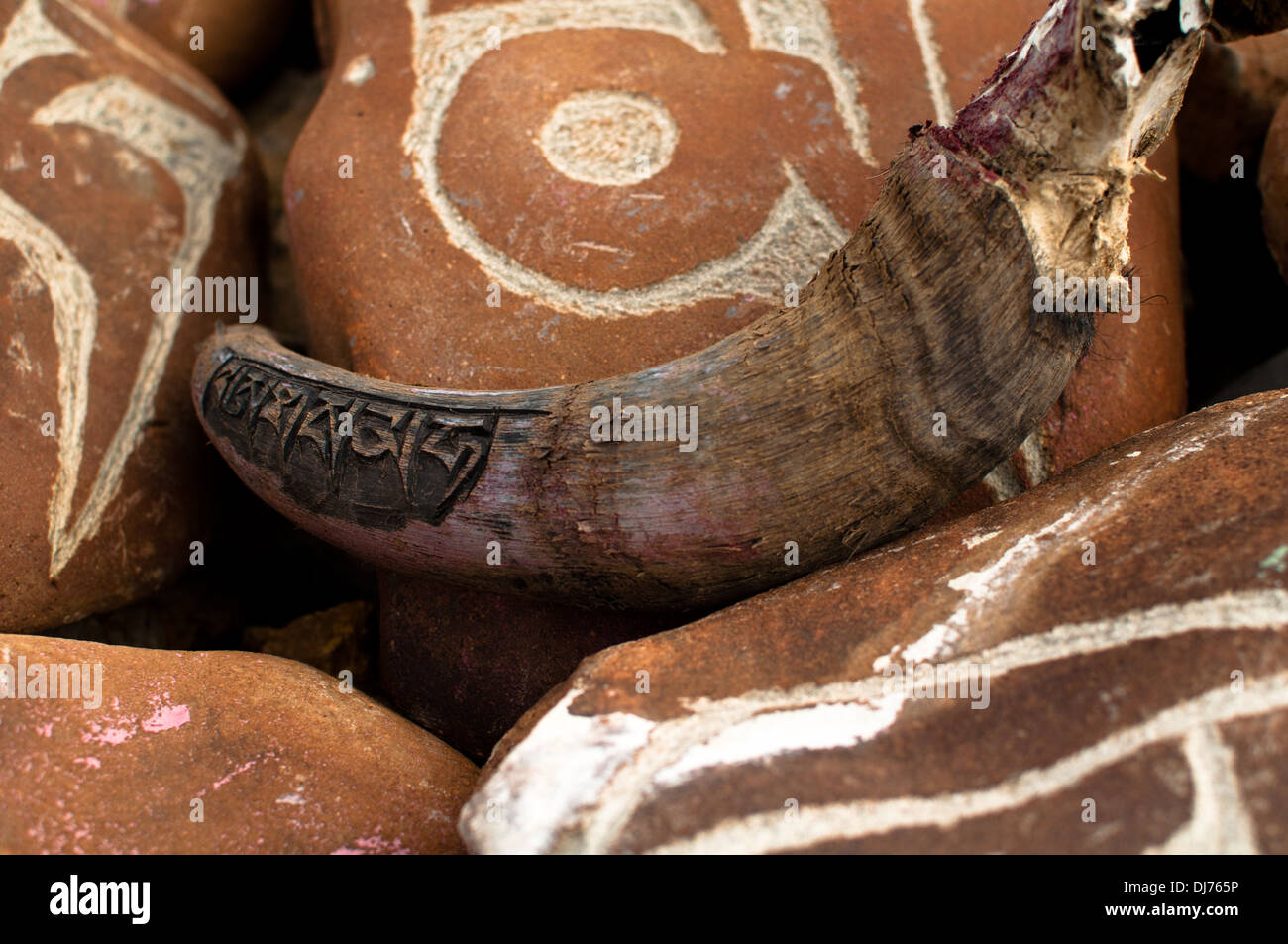
I have all sorts of different sized threaded rod, couplers, CF and brass tubing. It fit the hole in the bellcrank so I assumed it was okay.

I don't want to weaken the wing's integrity by cutting the sheeting, and I have plenty of assorted hardware that might solve it for me and be trustworthy. I'll think it over in the light of day first. One of the perils if my first 35 sized build. At the time it seemed like the right stuff. I have some 4-40 couplers, just that this wire is thinner than their hole. They work well, just be careful not to dollop any solder balls onto the wing. If you want to transition from wire to to a 4-40 clevis all you need to do is buy a solder 4-40 threaded coupler from the LHS. Cribbs74 wrote:Looks wonderful, I like the way the lucky boxes and hinges worked out.
